Il existe de nombreux types de feuilles de plastique offrant un large éventail d’utilisations.Actuellement, les principaux types sont le chlorure de polyvinyle, le polystyrène et le polyester (PET).La feuille PET a de bonnes performances et répond aux exigences nationales en matière d'indice d'hygiène pour les produits moulés et aux exigences internationales de protection de l'environnement.Ils appartiennent à la table de la protection de l'environnement.Actuellement, les emballages doivent répondre aux exigences de protection de l’environnement et de recyclage, c’est pourquoi la demande de feuilles PET est de plus en plus élevée.Cet article traite principalement du processus de production et des problèmes courants des feuilles PET.
Technologie de production de feuilles PET :
(1) feuille PET
Comme les autres plastiques, les propriétés des feuilles de PET sont étroitement liées au poids moléculaire.Le poids moléculaire est déterminé par la viscosité intrinsèque.Plus la viscosité intrinsèque est élevée, meilleures sont les propriétés physiques et chimiques, mais la mauvaise fluidité et la difficulté de mise en forme.Plus la viscosité intrinsèque est faible, plus les propriétés physiques et chimiques et la résistance aux chocs sont mauvaises.Par conséquent, la viscosité intrinsèque de la feuille de PET doit être de 0,8 dl/g à 0,9 dl/g.
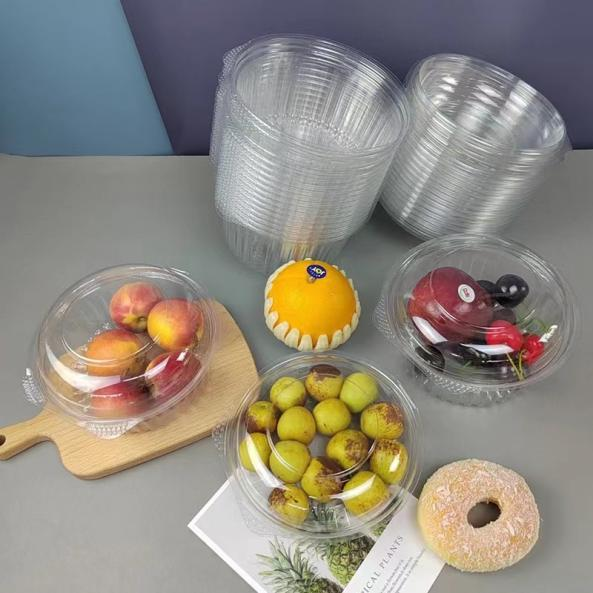
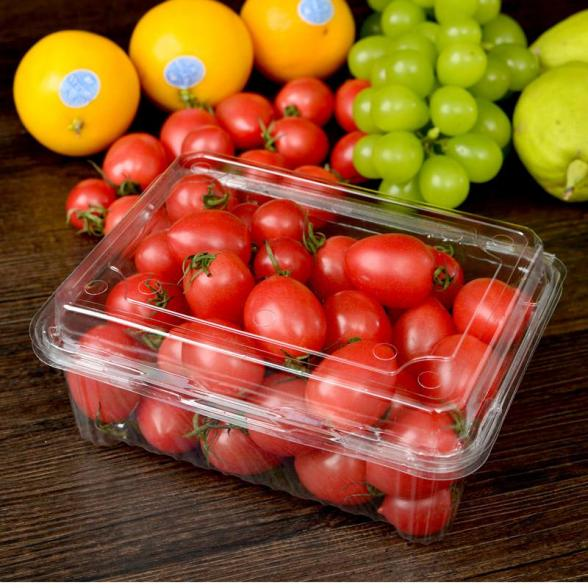
(2) Flux du processus de production
Le principaléquipement de production de feuilles PETcomprend des tours de cristallisation, des tours de séchage, des extrudeuses, des têtes de filière, des calandres à trois rouleaux et des bobineuses.Le processus de production est le suivant : cristallisation des matières premières-séchage-extrusion plastification-extrusion moulage-calandrage et façonnage-enroulement des produits.
1. Cristallisation.Les tranches de PET sont chauffées et cristallisées dans la tour de cristallisation pour aligner les molécules, puis augmenter la température de transition vitreuse des tranches pour éviter l'adhésion et le colmatage de la trémie pendant le processus de séchage.La cristallisation est souvent une étape indispensable.La cristallisation prend 30 à 90 minutes et la température est inférieure à 149°C.
2. Sécher.À haute température, l'eau hydrolysera et dégradera le PET, ce qui entraînera une réduction de son adhérence caractéristique, et ses propriétés physiques, notamment la résistance aux chocs, diminueront à mesure que le poids moléculaire diminue.Par conséquent, avant de fondre et d’extruder, le PET doit être séché pour réduire la teneur en humidité, qui doit être inférieure à 0,005 %.Le séchoir à déshumidification est utilisé pour le séchage.En raison de l'hygroscopique du matériau PET, lorsque l'eau pénètre profondément dans la surface de la tranche, des liaisons moléculaires se forment et une autre partie de l'eau pénètre profondément dans la tranche, ce qui rend le séchage difficile.Par conséquent, l’air chaud ordinaire ne peut pas être utilisé.Le point de rosée de l'air chaud doit être inférieur à -40 °C et l'air chaud pénètre dans la trémie de séchage par un circuit fermé pour un séchage continu.
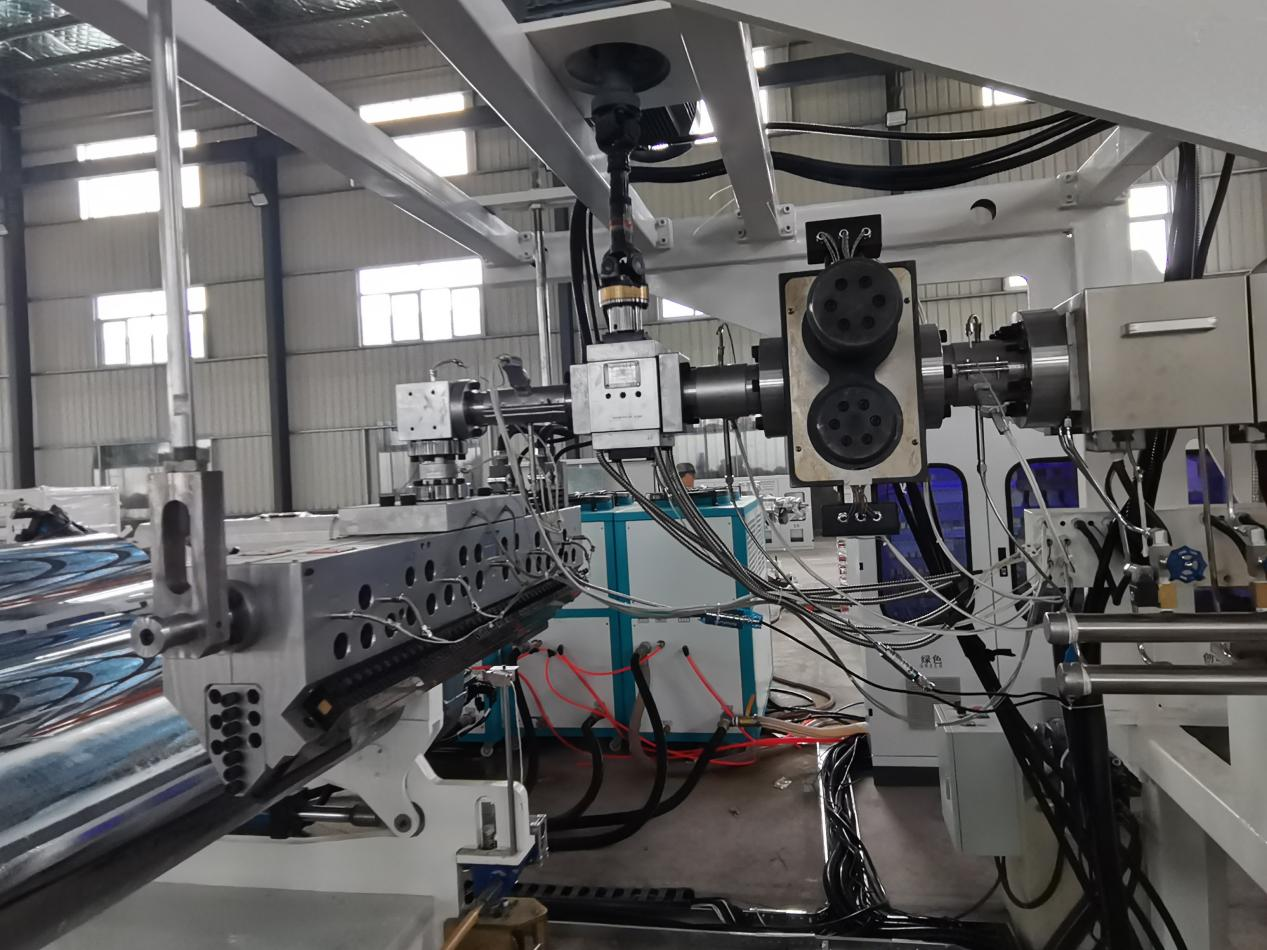
3. Pressez.Après cristallisation et séchage, le PET se transforme en polymère au point de fusion évident.La température de moulage du polymère est élevée et la plage de contrôle de la température est étroite.Une vis barrière spécifique au polyester est utilisée pour séparer les particules non fondues de la masse fondue, ce qui permet de maintenir un processus de cisaillement plus long et d'augmenter le rendement de l'extrudeuse.Adopte une matrice à lèvres flexible avec une tige d'accélérateur simplifiée.La tête du moule est effilée.Les glissières profilées et les lèvres de la matrice sans rayures indiquent que la finition devrait être bonne.Le chauffe-moule a des fonctions de drainage et de nettoyage.
4. Refroidissement et mise en forme.Une fois que la fonte est sortie de la tête, elle entre directement dans la calandre à trois rouleaux pour le calandrage et le refroidissement.La distance entre la calandre à trois rouleaux et la tête de la machine est généralement maintenue à environ 8 cm, car si la distance est trop grande, la planche s'affaissera et se froissera facilement, ce qui entraînera une mauvaise finition.De plus, en raison de la longue distance, la dissipation thermique et le refroidissement sont lents et le cristal devient blanc, ce qui n'est pas propice au roulement.L'unité de calandrage à trois rouleaux se compose de rouleaux supérieur, intermédiaire et inférieur.L'arbre du rouleau central est fixe.Pendant le processus de refroidissement et de calandrage, la température de surface du rouleau est de 40 °C à 50 °C.L'arbre des rouleaux supérieur et inférieur peut monter et descendre.
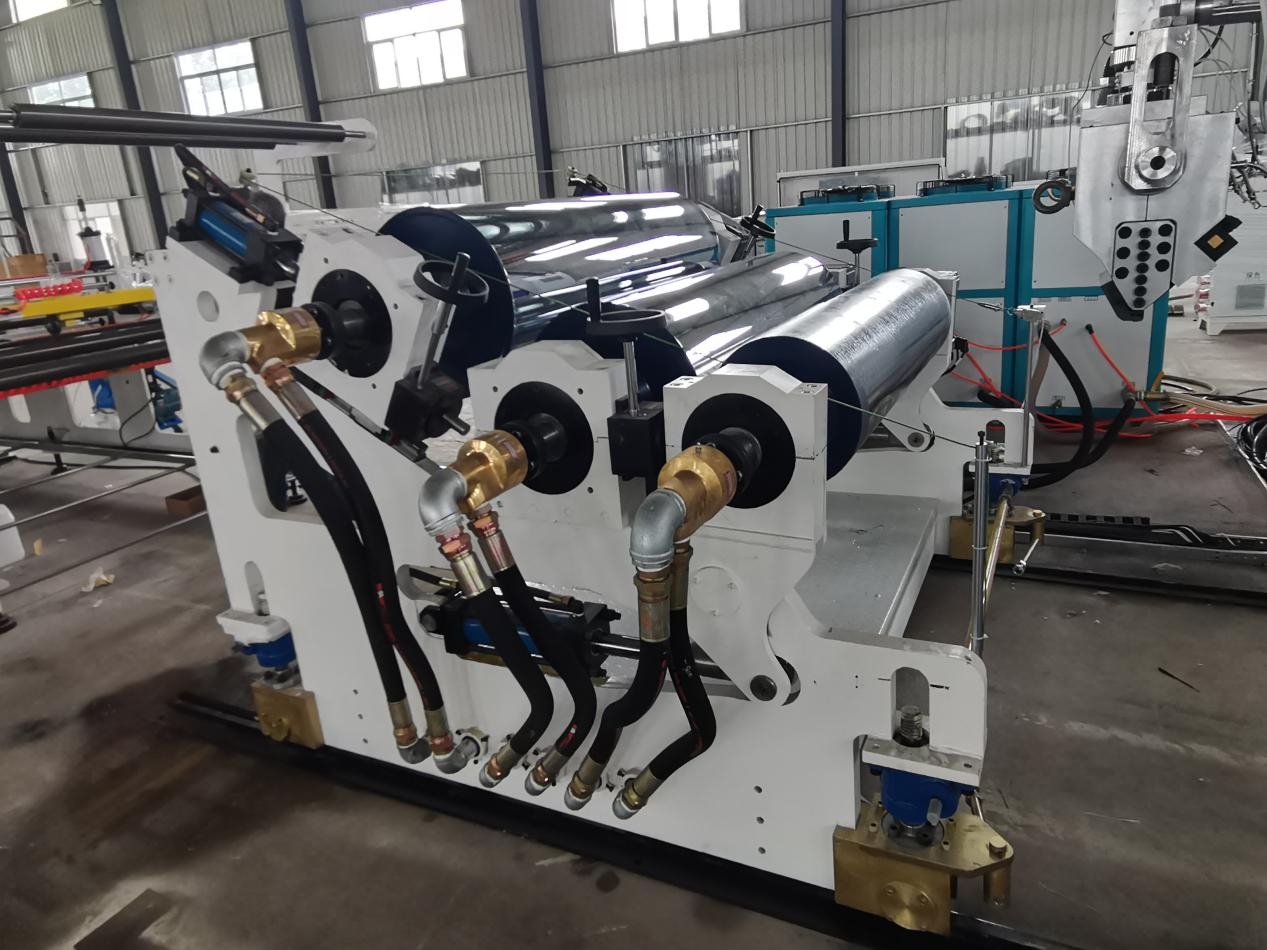
Heure de publication : 28 septembre 2023